Hydrogen peroxide, H₂O₂, is a versatile chemical that is used in a variety of applications. The older segment of our readers may remember their parents using dilute solutions of H₂O₂ to clean wounds. But disinfection is not the only use of H₂O₂. Industrially, because of its strong oxidation potential and its release of only H₂O and O₂ upon use, H₂O₂ is used as a chemical reagent (e.g., epoxidation, production of other oxidisers), bleaching of cellulosic materials (e.g., cotton and wood) and in wastewater treatment. Indeed, European industry uses 50% of the produced H₂O₂ in the chemical and pharmaceutical sectors, 41% in the pulp and paper sector and 8% in the textiles sector. The value of the global H₂O₂ market in 2023 was estimated to be USD 1.82 billion, with an anticipated compound annual growth rate of 3.8% from 2023 to 2032.
H₂O₂ production is globally dominated by the Riedl-Pfleiderer process, also known as the anthraquinone or auto-oxidation (AO) process. This process accounts for 95% of the worldwide H₂O₂ production and involves an indirect synthesis route that requires hydrogenation of an organic compound, anthraquinone, over a precious metal catalyst. Paradoxically, although H₂O₂ is not a carbon-containing chemical, fossil carbon is one of the key reagents in the AO process, since the hydrogen (H₂) required in the process is generated from the steam reforming of methane (natural gas). This H₂ production method has a significant CO₂ footprint; 0.54 tonne – 0.77 tonne CO₂ is generated per tonne 100% H₂O₂, just for the required H₂. Furthermore, since H₂O₂ is unstable, it must be shipped in diluted aqueous solutions from the centralised production facilities, further impacting its climate footprint. 50% or more of the transported material is just water!
For these reasons, greener, alternative production methods for H₂O₂ are under investigation. Preferably, H₂O₂ production should use electricity directly. In this way, renewable energy, which is provided as electricity, could be used without any intermediate steps, such as the electrolytic splitting of water to make H₂ and O₂. If the production could be done economically on a smaller scale, such a modular solution would eliminate the transportation requirements.
Different electrochemical production routes to H₂O₂ are under investigation. Most of these routes are based on the reduction of O₂ or the oxidation of water, sometimes in combination, and are mostly still in a development phase at laboratory scale. Electrochemical solutions are attractive since they provide the necessary operational flexibility for modular production. As one example, small, electrochemical units that make 5 kg H₂O₂ per day from only air, water and electricity are available. Unfortunately, these units produce only very diluted (0.5 %) H₂O₂ solutions, and neither the amount nor the concentration of H₂O₂ are suitable for industrial applications.
The HYPER project aims to produce H₂O₂ electrochemically (e-H₂O₂), although the technology under development will use a more robust, intermediate electrochemical process. This will lead to the production of e-H₂O₂ in quantities and concentrations that are relevant for use in pulp and paper mills, textile manufacturers, chemical industries and other larger scale applications, so that e-H₂O₂ can be produced when and where it is needed, from only electricity and water. The electrochemical intermediate will be recycled. Realisation of the HYPER process is expected to reduce the CO₂ footprint for H₂O₂ production by 75%, when compared to the AO process, when renewable electricity is used. Energy requirements are anticipated to be reduced by one-third. The ability of HYPER’s e-H₂O₂ to meet these targets will become clearer once the project commissions its TRL 6 reactor in 2026
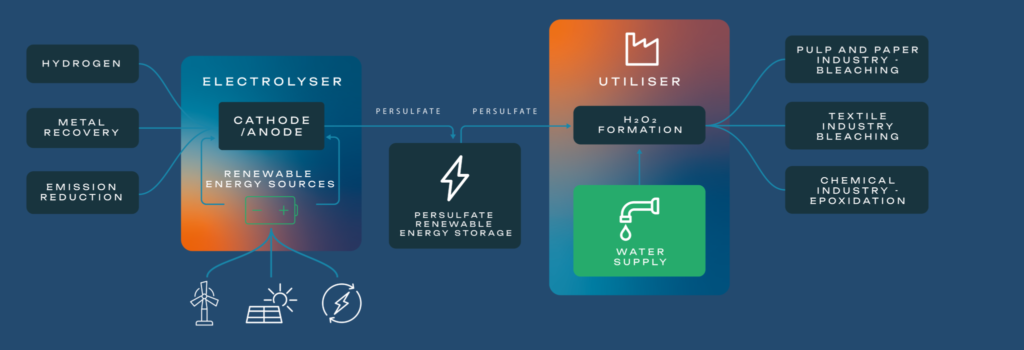